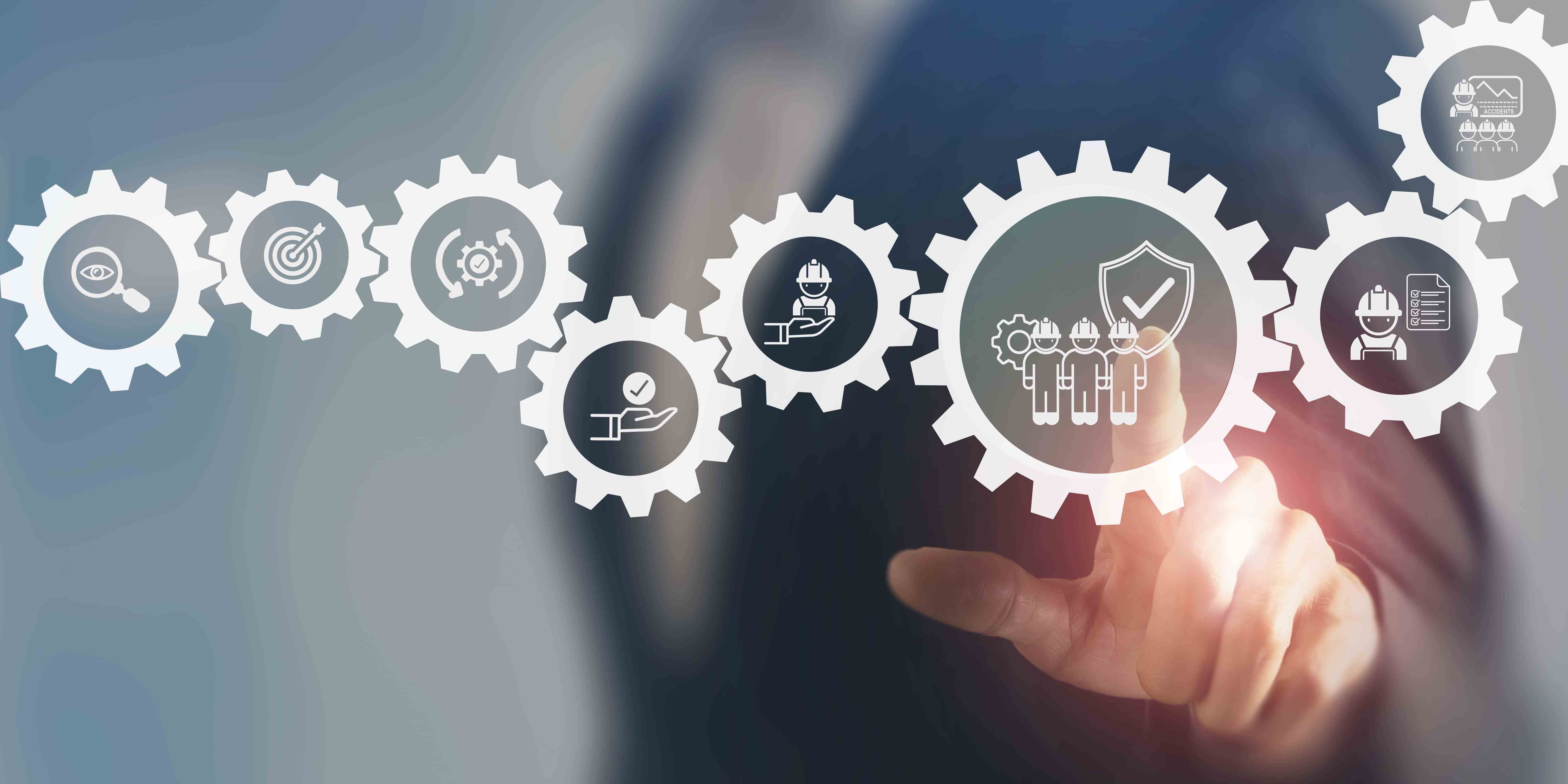
La productividad de las máquinas depende de sistemas de transmisión de potencia confiables. ¿Qué es un engranaje? Estos componentes mecánicos circulares transfieren movimiento y fuerza entre ejes giratorios mediante dientes que se entrelazan. Desde plantas de tratamiento de agua hasta instalaciones de procesamiento químico, los engranajes permiten un control preciso de la velocidad y la multiplicación del par motor. Comprender los diferentes tipos de engranajes ayuda a los ingenieros a seleccionar soluciones óptimas para aplicaciones industriales específicas, garantizando operaciones eficientes en los entornos de fabricación.
Entendiendo los fundamentos de los engranajes
Lo que es un engranaje se vuelve más claro cuando se examina su función principal. Estos dispositivos mecánicos consisten en ruedas dentadas que se acoplan entre sí, transmitiendo el movimiento rotacional de un eje a otro. El principio fundamental se basa en el contacto entre los dientes del engranaje, lo que previene el deslizamiento y proporciona características de transmisión positiva.
Cómo funcionan los engranajes implica varios principios mecánicos. Cuando un engranaje gira, sus dientes empujan contra los dientes del engranaje emparejado, lo que provoca la rotación en la dirección opuesta. La relación de engranaje determina las relaciones de velocidad y par entre los ejes de entrada y salida. Los engranajes más pequeños que impulsan a los más grandes reducen la velocidad mientras aumentan el par. Por el contrario, los engranajes más grandes que impulsan a los más pequeños aumentan la velocidad pero reducen el par.
Principios operativos clave:
- Reducción de velocidad: El engranaje pequeño impulsa al engranaje grande = salida más lenta, mayor par motor
- Aumento de velocidad: El engranaje grande impulsa al engranaje pequeño = salida más rápida, menor par motor
- Cambio de dirección: Los engranajes que se acoplan giran en direcciones opuestas
- Conservación de energía: La potencia de entrada es igual a la potencia de salida menos las pérdidas por fricción
- Transmisión positiva: El acoplamiento dentado previene el deslizamiento bajo carga
La ventaja mecánica ocurre a través de esta relación velocidad-par. Una relación de engranaje de 4:1 significa que el eje de entrada rota cuatro veces por cada rotación de salida. Esta configuración multiplica el par motor por cuatro mientras reduce la velocidad de salida por el mismo factor. La conservación de energía asegura que la potencia se mantenga constante, menos las pérdidas por fricción.
Los dientes de los engranajes deben mantener un contacto adecuado a lo largo de la rotación. El perfil de diente evolvente, utilizado en la mayoría de las aplicaciones industriales, proporciona un acoplamiento suave y una transferencia de movimiento constante. El espaciamiento adecuado, llamado paso, asegura una distribución uniforme de la carga a través de varios dientes simultáneamente.
Las calificaciones de eficiencia generalmente oscilan entre el 95% y el 99% para sistemas de engranajes de calidad. Las pérdidas ocurren debido a la fricción deslizante entre las superficies de los dientes, la fricción de los rodamientos y la resistencia al aire a altas velocidades. La lubricación reduce estas pérdidas mientras extiende la vida útil de los componentes.
Clasificaciones principales de engranajes
Los tipos de engranajes se dividen en tres categorías principales según la disposición de los ejes. Cada categoría sirve para aplicaciones específicas donde la orientación del eje y las limitaciones de espacio dictan la elección óptima.
Engranajes de eje paralelo
Los engranajes rectos representan el diseño más simple de mecanismo de engranaje. Estos engranajes cuentan con dientes rectos paralelos al eje del eje. Los costos de fabricación se mantienen bajos debido a los requisitos de mecanizado simples. Los engranajes rectos sobresalen en aplicaciones que requieren una sincronización precisa, como sistemas de transporte y equipos de manipulación de materiales.
Los engranajes helicoidales ofrecen un rendimiento mejorado en comparación con los diseños de engranajes rectos. Los dientes en ángulo crean un acoplamiento gradual que reduce el ruido y la vibración. Las instalaciones de fabricación eligen los engranajes helicoidales para aplicaciones donde la operación suave es más importante que el costo. Los dientes en ángulo distribuyen las cargas a través de varios dientes simultáneamente, aumentando la capacidad de carga.
Engranajes de ejes intersectados
Los engranajes cónicos rectos manejan intersecciones de ejes a 90 grados. Estos engranajes cuentan con dientes rectos que convergen hacia el punto de intersección del eje. Los equipos de minería y la maquinaria agrícola utilizan comúnmente engranajes cónicos rectos, donde la construcción robusta es más importante que las consideraciones de ruido.
Los engranajes cónicos espirales ofrecen un rendimiento mejorado a través de dientes curvados. El diseño en espiral permite un acoplamiento gradual de los dientes, reduciendo las cargas de impacto y el ruido. Los diferenciales automotrices y los sistemas de transmisión industrial se benefician del funcionamiento suave y la mayor capacidad de carga de los engranajes cónicos espirales.
Engranajes de ejes no intersectados
Los engranajes sin fin sobresalen en aplicaciones de alta reducción. El gusano (engranaje en forma de tornillo) impulsa una rueda sin fin, logrando relaciones de 10:1 a 100:1 en una sola etapa. Las características de auto-bloqueo previenen el retroceso, lo que hace que los engranajes sin fin sean ideales para equipos de elevación y sistemas de transporte. Los sistemas reductores de engranajes químicos a menudo incorporan engranajes sin fin para aplicaciones de dosificación precisa de productos químicos, donde las tasas de flujo constantes son críticas.
Los engranajes hipoides manejan ejes no intersectados y desplazados. El eje del piñón se desplaza desde el centro del engranaje, lo que permite diseños más compactos. Los equipos industriales de alta resistencia utilizan engranajes hipoides cuando las limitaciones de espacio impiden la disposición estándar de los engranajes cónicos.
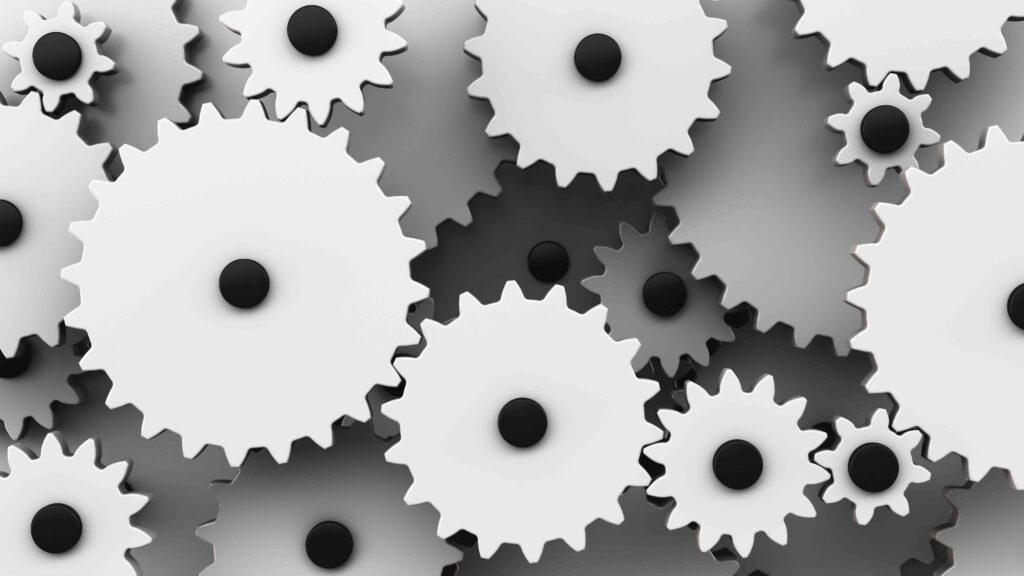
Sistemas de engranajes especializados
Los tipos de engranajes van más allá de las configuraciones básicas e incluyen sistemas especializados que abordan requisitos industriales únicos. Estos sistemas avanzados combinan múltiples engranajes para lograr características de rendimiento específicas.
Sistemas de engranajes planetarios
Los engranajes planetarios consisten en un engranaje central (engranaje solar), múltiples engranajes planetarios y un engranaje anular exterior. Esta disposición de los engranajes ofrece soluciones compactas y de alto par. El portador que sostiene los engranajes planetarios puede funcionar como entrada, salida o miembro estacionario, permitiendo diferentes relaciones de velocidad.
Las cajas de engranajes de turbinas eólicas ejemplifican las aplicaciones de engranajes planetarios. Múltiples etapas planetarias aumentan la rotación del rotor de baja velocidad hasta las velocidades del generador. El diseño compacto se ajusta dentro de las góndolas de las turbinas mientras maneja enormes pares de fuerzas del viento.
Los mezcladores industriales utilizan accionamientos planetarios para aplicaciones de mezcla de alta resistencia. Los múltiples caminos de carga a través de los engranajes planetarios distribuyen las fuerzas de manera uniforme, evitando el desgaste prematuro. Las capacidades de velocidad variable permiten un control preciso de los procesos de mezcla.
Sistemas de cremallera y piñón
Las aplicaciones de movimiento lineal requieren sistemas de cremallera y piñón. El piñón (engranaje circular) se acopla con una cremallera lineal, convirtiendo el movimiento rotatorio en movimiento lineal. Las herramientas de máquina CNC utilizan accionamientos de cremallera y piñón para un posicionamiento preciso a lo largo de los ejes lineales.
Los sistemas de automatización se benefician de la precisión de la cremallera y el piñón. Los operadores de puertas, sistemas de elevación y equipos de manipulación de materiales logran un posicionamiento preciso a través de estos sistemas. La conexión mecánica directa elimina el retroceso común en los accionamientos de tornillo.
Engranajes internos
Los engranajes internos tienen los dientes cortados dentro de un anillo, que se acoplan con piñones externos. Este diseño de configuración de engranajes crea arreglos compactos donde las limitaciones de espacio impiden la colocación de engranajes externos. Los sistemas planetarios utilizan frecuentemente engranajes de anillo internos como el miembro estacionario o de salida.
Los accionamientos de bombas utilizan engranajes internos para arreglos que ahorran espacio. El diseño concéntrico reduce el tamaño general del sistema mientras mantiene las relaciones de velocidad requeridas. Los engranajes internos también invierten la dirección de rotación sin engranajes adicionales.
Configuraciones y diseño de dientes de engranajes
Los tipos de dientes de engranajes determinan las características de rendimiento y la idoneidad para aplicaciones. La geometría del diente afecta la capacidad de carga, la generación de ruido y los requisitos de fabricación.
Configuraciones comunes de dientes de engranajes:
- Perfil evolvente: Elección estándar industrial para relaciones de velocidad consistentes
- Perfil cicloidales: Aplicaciones de precisión que requieren un tiempo exacto
- Ángulo de presión de 20 grados: Capacidad de carga equilibrada y fuerzas de empuje
- Ángulo de presión de 14.5 grados: Menor empuje, capacidad de potencia reducida
Ángulo de presión de 25 grados: Cargas más altas, fuerzas de empuje aumentadas
Los perfiles de dientes evolventes dominan las aplicaciones industriales. La curva matemática asegura relaciones de velocidad constantes y una transmisión de potencia suave. Los sistemas evolventes estandarizados permiten la intercambiabilidad entre los engranajes de diferentes fabricantes.
Los ángulos de presión, típicamente de 20 grados, definen las características de la forma de los dientes. Los ángulos de presión más altos aumentan la capacidad de carga pero generan más fuerzas de empuje. Los ángulos más bajos reducen el empuje pero limitan la capacidad de transmisión de potencia.
Los tipos de dientes de engranajes también incluyen perfiles cicloidales para aplicaciones especializadas. Los mecanismos de relojería y los instrumentos de precisión utilizan dientes cicloidales donde el tiempo exacto es más importante que la transmisión de potencia. Estos perfiles eliminan la fricción deslizante pero requieren una fabricación precisa.
Los sistemas de módulos estandarizan las relaciones del tamaño de los dientes. Los módulos métricos especifican el diámetro de paso dividido por el número de dientes. Los módulos estándar garantizan la compatibilidad entre los engranajes de diferentes fabricantes, mientras simplifican los cálculos de diseño.0
Los tratamientos superficiales mejoran el rendimiento de los engranajes. La cementación aumenta la dureza superficial mientras mantiene núcleos resistentes. La nitruración ofrece una excelente resistencia al desgaste para aplicaciones de alta carga. El granallado mejora la resistencia a la fatiga al introducir tensiones compresivas.
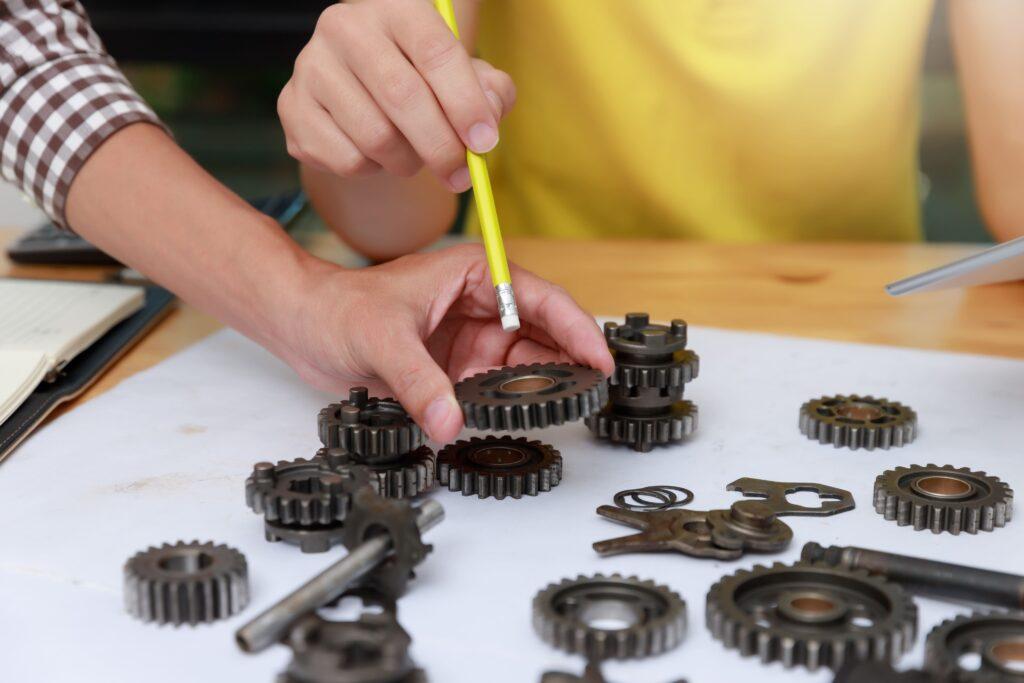
Aplicaciones industriales por tipo de engranaje
Los tipos de engranajes sirven a diversos sectores industriales, cada uno de los cuales requiere características de rendimiento específicas. Comprender los requisitos de la aplicación guía la selección adecuada de engranajes para obtener resultados óptimos.
Fabricación y producción
Los sistemas de transporte por cintas dependen en gran medida de los diseños de mecanismos de engranajes para un transporte confiable de materiales. Los engranajes rectos manejan aplicaciones de carga ligera donde el costo es lo más importante. Los engranajes helicoidales sirven para transportadores de alta resistencia que requieren una operación suave y una alta capacidad de carga.
Las máquinas herramienta exigen un control preciso del movimiento. Las máquinas de engranaje utilizan trenes de engranajes para una rotación precisa de la pieza de trabajo durante las operaciones de corte de engranajes. Las relaciones de engranajes deben mantener relaciones exactas para producir dientes de engranaje precisos.
Los sistemas robóticos requieren accionamientos compactos y precisos. Los engranajes planetarios encajan dentro de los espacios de las articulaciones mientras proporcionan la reducción de velocidad necesaria. La eliminación del retroceso asegura un posicionamiento preciso para las operaciones de ensamblaje.
Industrias de procesos
El equipo de procesamiento químico opera en entornos difíciles que requieren una transmisión de potencia confiable. Los engranajes de acero inoxidable resisten la corrosión de los productos químicos del proceso. Las cajas de engranajes cerradas protegen los componentes internos de la contaminación, mientras permiten una operación segura en áreas con materiales peligrosos.
Las instalaciones de tratamiento de agua utilizan accionamientos de engranajes para operaciones de bombas, sistemas de mezcla y equipos de filtración. La capacidad de velocidad variable permite la optimización del proceso según los requisitos de flujo y los objetivos de tratamiento.
La producción de alimentos exige diseños sanitarios que cumplan con los requisitos de la FDA. Las superficies lisas previenen el crecimiento bacteriano, mientras que las capacidades de lavado permiten una limpieza a fondo. Los accionamientos cerrados previenen la contaminación de los productos alimenticios.
Generación de energía
Las cajas de engranajes de turbinas eólicas representan algunas de las aplicaciones de engranajes industriales más grandes. Múltiples etapas aumentan las velocidades del rotor de 20-50 RPM a las velocidades del generador de 1500-1800 RPM. Las cargas extremas y las condiciones ambientales requieren diseños y materiales especializados.
Los sistemas de accionamiento de generadores utilizan acoplamientos de engranajes para conectar los motores primarios con los generadores eléctricos. Los acoplamientos flexibles permiten el desalineamiento de los ejes mientras transmiten toda la potencia. Los programas de mantenimiento se coordinan con las revisiones de generadores para minimizar el tiempo de inactividad.
Las plantas hidroeléctricas emplean sistemas de engranajes para los operadores de compuertas y el control de turbinas. Las capacidades de posicionamiento preciso permiten un control óptimo del flujo de agua para una máxima eficiencia en la generación de energía.
Selección de engranajes y consideraciones de rendimiento
La selección adecuada de configuraciones de engranajes requiere analizar múltiples factores de rendimiento. Los requisitos de carga, las relaciones de velocidad y el entorno operativo influyen en la elección óptima de los engranajes.
Criterios esenciales de selección:
- Capacidad de carga: Requisitos de servicio continuo frente a intermitente
- Relaciones de velocidad: Reducciones de una sola etapa (hasta 6:1) frente a múltiples etapas
- Entorno operativo: Temperatura, humedad, condiciones corrosivas
- Limitaciones de ruido: Helicoidal para operación silenciosa, recto para economía
- Limitaciones de espacio: Planetario para diseños compactos, eje paralelo para accesibilidad
Acceso para mantenimiento: Disposiciones de engranajes cerrados frente a abiertos
Los ciclos de trabajo afectan significativamente la vida útil de los engranajes. La operación continua requiere engranajes de mayor calidad en comparación con el servicio intermitente. El análisis de la distribución de carga asegura factores de seguridad adecuados para la vida útil esperada.
Las relaciones de velocidad determinan la selección del tipo de engranaje. Las reducciones de una sola etapa hasta 6:1 favorecen los engranajes rectos o helicoidales. Las relaciones más altas requieren múltiples etapas o tipos especializados como los engranajes sin fin.
Los factores ambientales influyen en la selección de materiales y medidas de protección. Las atmósferas corrosivas requieren acero inoxidable o recubrimientos protectores. Las altas temperaturas exigen lubricantes especiales y consideraciones de tratamiento térmico.
Los requisitos de ruido afectan la selección del tipo de engranaje. Los engranajes helicoidales generan menos ruido que los engranajes rectos debido al acoplamiento gradual de los dientes. La fabricación de precisión reduce el ruido mediante acabados de superficie mejorados y tolerancias más estrictas.
Las consideraciones de costo equilibran la inversión inicial contra los gastos operativos. Los engranajes de mayor calidad tienen un costo inicial más alto, pero proporcionan una vida útil más larga y requieren menos mantenimiento. El análisis del costo del ciclo de vida guía la selección óptima.
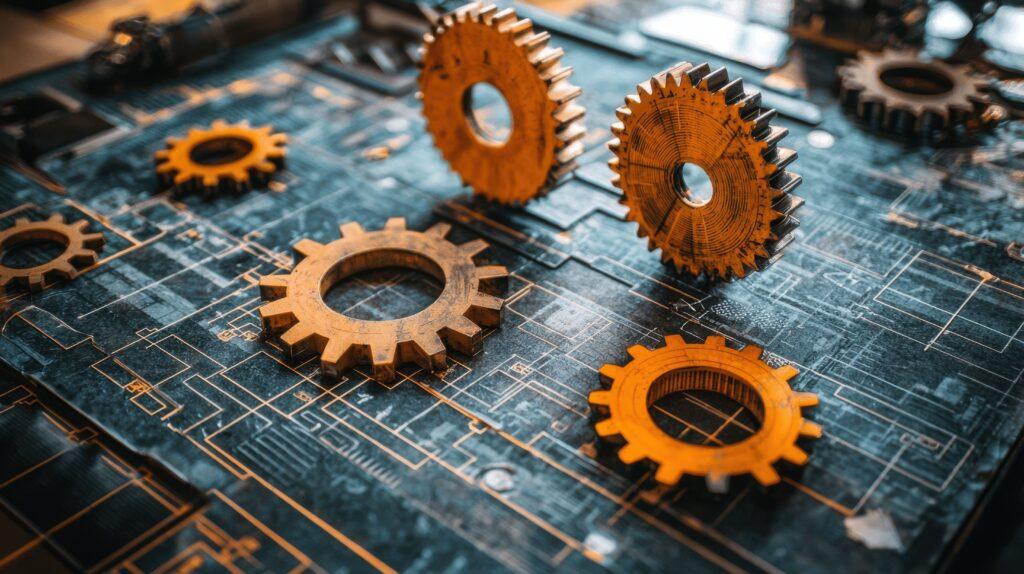
Requisitos de mantenimiento y servicio
Un mantenimiento adecuado garantiza el funcionamiento confiable del mecanismo de engranajes durante toda su vida útil. La lubricación, la inspección y las reparaciones oportunas previenen fallos catastróficos y extienden la vida útil de los componentes.
Mejores prácticas de mantenimiento:
Lubricación regular: Sistemas de baño de aceite para unidades cerradas, grasa para engranajes abiertos
- Monitoreo de vibraciones: Análisis de frecuencia para detectar problemas en desarrollo
- Inspección visual: Verificar patrones de desgaste uniforme y alineación correcta
- Análisis de aceite: Monitorizar los niveles de contaminación y el contenido de partículas de desgaste
- Monitoreo de temperatura: Detectar sobrecalentamiento debido a una lubricación inadecuada
Análisis de carga: Verificar que las cargas operativas permanezcan dentro de los límites de diseño
Los requisitos de lubricación varían según el tipo de engranaje y las condiciones de operación. Los sistemas de baño de aceite son adecuados para cajas de engranajes cerradas que operan a velocidades moderadas. La lubricación con grasa sirve para engranajes abiertos y aplicaciones de baja velocidad. Los lubricantes sintéticos extienden los intervalos de servicio y mejoran el rendimiento a altas temperaturas.
Los patrones de desgaste indican las condiciones operativas y los problemas potenciales. El desgaste uniforme en las caras de los dientes indica una alineación y carga adecuadas. El desgaste localizado sugiere desalineación, sobrecarga o lubricación inadecuada.
El monitoreo de vibraciones detecta problemas en desarrollo antes de que ocurra una falla. El análisis de frecuencia identifica frecuencias específicas de acoplamiento de engranajes y contenido armónico. El análisis de tendencias realiza un seguimiento de las tasas de deterioro para programar el mantenimiento planificado.
Los servicios profesionales de engranajes proporcionan experiencia especializada para sistemas de engranajes complejos. Los técnicos experimentados entienden los modos de fallo y las técnicas de reparación específicas para diferentes tipos de engranajes. Las inspecciones regulares identifican problemas temprano, evitando costosas reparaciones de emergencia y el tiempo de inactividad de la producción.
Los programas de mantenimiento preventivo se coordinan con los requisitos de producción. El análisis de aceite detecta contaminación y partículas de desgaste, lo que indica el estado de los componentes. Las sustituciones programadas previenen fallos inesperados durante períodos críticos de producción.
Tendencias futuras en la tecnología de engranajes
Los materiales avanzados continúan mejorando el rendimiento y la durabilidad de los engranajes. La metalurgia en polvo permite formas complejas imposibles de lograr con el mecanizado tradicional. Los plásticos reforzados con fibra de carbono reducen el peso en aplicaciones aeroespaciales, manteniendo los requisitos de resistencia.
Los sistemas de monitoreo inteligente integran sensores directamente en los sistemas de engranajes. La tecnología inalámbrica transmite datos de vibración, temperatura y carga para monitoreo en tiempo real de las condiciones. El análisis predictivo identifica el momento óptimo para el mantenimiento basado en las condiciones reales de los componentes, en lugar de los horarios establecidos.
La fabricación aditiva abre nuevas posibilidades para el diseño y la producción de engranajes. La impresión 3D permite la creación rápida de prototipos de geometrías complejas. La producción en pequeñas series se vuelve económica para aplicaciones especializadas que requieren configuraciones únicas de engranajes.
Optimización de sus sistemas de engranajes
Comprender los tipos de engranajes permite tomar decisiones informadas para aplicaciones industriales. Cada tipo de engranaje ofrece ventajas específicas adecuadas a condiciones operativas particulares y requisitos de rendimiento. La selección adecuada considera los requisitos de carga, las relaciones de velocidad, los factores ambientales y las capacidades de mantenimiento. Cómo funcionan los engranajes a través de principios mecánicos sigue siendo constante, pero las aplicaciones continúan expandiéndose a medida que avanza la tecnología. La experiencia profesional garantiza una selección y mantenimiento óptimos de los engranajes para operaciones industriales confiables y eficientes.
Trabajar con proveedores experimentados proporciona acceso a conocimientos especializados y componentes de calidad. AMED-US ofrece soluciones completas de engranajes respaldadas por décadas de experiencia industrial en diversas aplicaciones en toda América.